
Diecasting starts with the preparation of high-quality steel molds, commonly referred to as dies. Dies are constructed for the harsh pressures and temperatures of molten metal. These dies are meticulously crafted to preserve intricate detail and maintain tight tolerances, ensuring that each cast part conforms to specific specifications for design. During the casting process, metals like aluminum, zinc, magnesium, and copper melt and are in the cavity of the die with high pressures. This rapid injection and subsequent cooling results in components which have excellent dimensions and an even surface. The precision of the dies permits the making of complex components, which are often unattainable by other methods of manufacturing.
One of the main benefits of diecasting is its effectiveness in mass production. Once the dies are fabricated this process is able to be repeated hundreds or thousands times with minimal variation between the components. This high repeatability is crucial in industries that need large numbers of components that are identical. Additionally, diecasting is known for its material efficiency. It produces less waste compared to other techniques for forming metal in that excess metal could be recycled and used again. This not only reduces the cost of material but also contributes to environmentally sustainable manufacturing methods. Combining accuracy, speed and material efficiency makes diecasting an attractive solution for manufacturing large quantities.
Diecasting has many benefits in terms of physical properties and efficiency. Diecast components are well-known as durable and strong as they are the most important qualities for parts that are used for demanding tasks. Fine-grain formation that occurs as a result of the fast cooling process the material contributes to these properties that make diecast products suitable to be used in high-stress environments. Furthermore, the process of diecasting permits the inclusion of thin walls and complicated components without harming the strength of the finished item. This feature is particularly beneficial in aerospace and automotive industries, where weight reduction whilst maintaining strength and structural integrity is vital to increase fuel efficiency and overall performance. To get further information please go to Senadiecasting
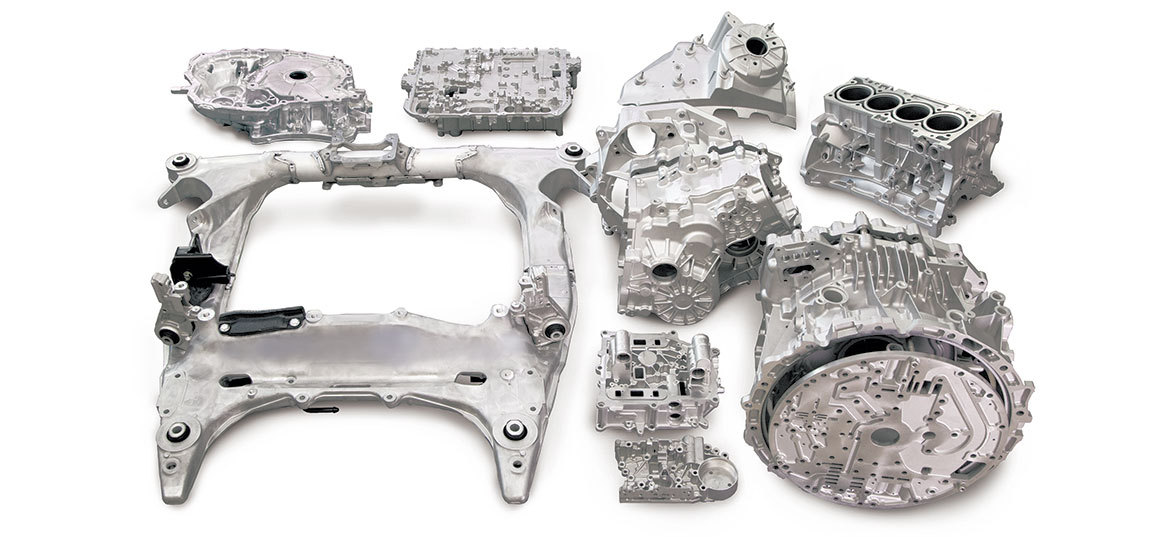
The materials you choose for diecasting significantly influences the properties and functionality of the final product. Aluminum is a popular choice due to its excellent strength-to-weight ratio, its resistance to corrosion and thermal and electrical conductivity. These qualities make aluminum an ideal choice for automotive and aerospace applications where weight reduction is a major concern. Zinc alloys offer high strength and ductility. They are appropriate for products that need fine detail and long-lasting. Magnesium alloys have the tiniest weight of metallic structural elements, offering an advantage in applications where weight reduction is crucial. Copper alloys are more rarely used, are valued for their excellent electrical conductivity as well as durability to corrosion. Each metal has unique advantages making it possible for manufacturers to pick the most suitable option to meet the application they are looking for.
Diecasting stands at the top of technology for manufacturing, providing an unbeatable blend of precision efficacy, and flexibility that is unmatched by other manufacturing processes. Its capacity to produce complex, high-quality components with exceptional mechanical properties makes it a vital component in various sectors ranging from automotive to consumer electronic products. The efficiency and material savings inherent in the diecasting process demonstrate its worth in high-volume manufacturing. Its flexibility guarantees that it is able to accommodate the changing demands of modern manufacturing. As industries continue to push limits of innovation and efficiency, diecasting will continue to be an essential tool providing the basis for advancements, and also facilitating the development of new products that will shape our future.